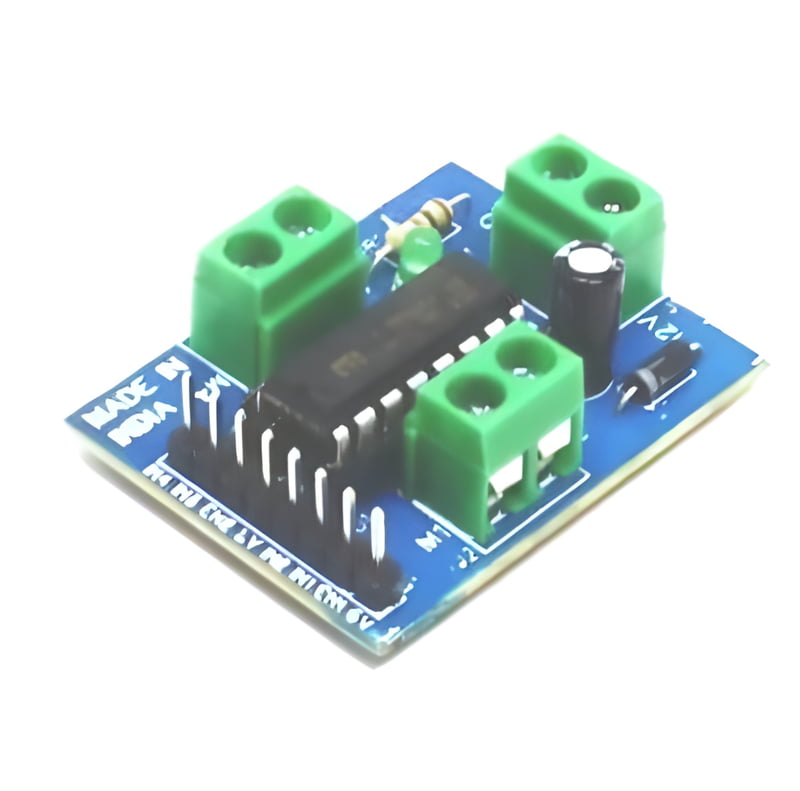
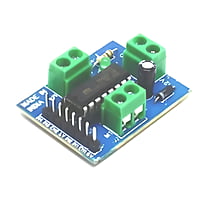
L293D Motor Control Driver
Available Offer
Share :
Key Features:-
Dual H-Bridge Configuration: The L293D IC is designed as a dual H-bridge motor driver. Each H-bridge can control one DC motor, allowing you to control the direction of rotation (forward and reverse) and the speed of the motor.
High Current Handling: The L293D is capable of handling relatively high currents, making it suitable for driving motors with moderate power requirements. This feature is essential for applications like mobile robots and small vehicles.
Bidirectional Control: The IC enables bidirectional control of the motors, allowing you to move them both forward and backward.
Four Input Pins: For each H-bridge, there are four input pins:
- Enable (EN): Used to enable or disable the motor connected to the H-bridge.
- Input 1 (IN1) and Input 2 (IN2): These pins determine the motor's direction.
- Input 3 (IN3) and Input 4 (IN4): These pins control the motor's speed using pulse-width modulation (PWM) signals.
Built-in Diodes: The L293D includes flyback diodes (also called freewheeling diodes) to protect against voltage spikes that can occur when a motor is turned off.
Wide Operating Voltage Range: It can operate over a wide voltage range, typically from 4.5V to 36V, making it compatible with a variety of power sources.
Functionality:
- The L293D motor control driver simplifies the process of controlling DC motors by providing an easy-to-use interface for microcontrollers and other control devices.
- When a specific combination of input signals is applied to the control pins, the IC will drive the connected motor in the desired direction at a specific speed.
- By using PWM signals on the input pins associated with speed control (IN3 and IN4 for one H-bridge and IN1 and IN2 for the other), you can achieve variable motor speeds.
Applications:
- Mobile Robots: It is used to control the motors of wheeled robots for movement.
- RC Cars and Vehicles: In remote-controlled vehicles to control motor speed and direction.
- Automation Systems: For controlling the movement of conveyor belts, automatic doors, and other machinery.
- Electronics Projects: In hobby and DIY electronics projects requiring motor control.
- Prototyping: It is a common choice for motor control when prototyping electronic designs.